CNC in 3D printing represents a powerful synergy between automation and additive manufacturing, offering unparalleled precision, efficiency, and material versatility. As technology advances, its integration will drive innovations across various industries, shaping the future of manufacturing. Whether for rapid prototyping or full-scale production, CNC-driven 3D printing is a game-changer in the evolution of industrial fabrication. While challenges remain, ongoing research and development promise to overcome limitations, further solidifying the role of CNC in the 3D printing revolution.
Continue readingHybrid Manufacturing in 3D Printing: The Future of Advanced Manufacturing
Excepteur sint occaecat cupidatat non proident, sunt in culpa qui officia deserunt mollit anim idest borum Sed ut perspiciatis unde omnis iste natus error sit voluptatem accusantium doloremque laudantium totam rem aperiam, eaque ipsa quae ab illo inventore veritatis.
Continue readingLow Volume Manufacturing in 3D Printing: A Game-Changer for Production
Introduction
Low volume manufacturing is becoming an essential approach for industries looking to produce high-quality, cost-effective, and customised products in small quantities. With the rise of 3D printing, manufacturers now have an efficient, flexible, and scalable solution for low-volume production. This article explores the concept of low-volume manufacturing in 3D printing, its advantages, applications, challenges, and future trends.
What is Low Volume Manufacturing?
Low volume manufacturing refers to the production of a limited number of parts or products, typically ranging from a few dozen to several thousand units. Unlike mass production, which focuses on large-scale manufacturing, low-volume production is ideal for custom, on-demand, and specialised production needs.
3D printing, also known as additive manufacturing (AM), plays a crucial role in low-volume manufacturing. It allows manufacturers to build components layer by layer, reducing material waste, setup time, and production costs.
Benefits of Low Volume Manufacturing in 3D Printing
1. Cost Efficiency for Small Runs
Traditional manufacturing methods, such as injection moulding and CNC machining, require expensive tooling and setup.
3D printing eliminates the need for costly moulds, making it economically viable for low-quantity production.
2. Faster Time-to-Market
No tooling or extensive setup is required, allowing manufacturers to move from design to production rapidly.
Ideal for prototyping and iterative product development, reducing lead times.
3. Customisation & Personalisation
3D printing enables highly customised and unique designs for specific customer needs.
Ideal for industries requiring tailored solutions, such as healthcare, aerospace, and automotive.
4. Reduced Material Waste
Traditional subtractive manufacturing results in significant material waste.
Additive manufacturing only uses material where needed, reducing costs and promoting sustainability.
5. On-Demand Production & Inventory Reduction
No need for large-scale warehousing, as products can be manufactured on demand.
Helps companies maintain lean inventory management, reducing overhead costs.
Key Applications of Low Volume 3D Printing Manufacturing
1. Prototyping and Product Development
3D printing is widely used for rapid prototyping, allowing designers to create functional models before final production.
Companies can test multiple design iterations quickly, improving efficiency and product quality.
2. Custom Medical Devices and Healthcare Applications
Custom prosthetics, implants, and dental devices are tailored to individual patients.
3D bioprinting is emerging for tissue engineering and organ research.
3. Aerospace and Automotive Industries
3D printing allows the creation of lightweight, complex components for aerospace and automotive applications.
Enables production of replacement parts, specialised tools, and functional end-use components.
4. Consumer Goods and Wearables
Fashion, jewellery, and footwear companies utilise 3D printing for unique and limited-edition products.
Enables brands to offer personalisation and exclusive designs to customers.
5. Industrial Tooling and Fixtures
Manufacturers use 3D printing for custom jigs, fixtures, and tooling, reducing the need for expensive machining.
Improves production efficiency and reduces downtime in manufacturing.
Challenges of Low Volume Manufacturing in 3D Printing
1. Material Limitations
Some industries require specific high-strength or heat-resistant materials that may not yet be widely available in 3D printing.
Advances in metal and composite materials are addressing this challenge.
2. Surface Finish & Post-Processing Needs
3D-printed parts often require post-processing, such as sanding, polishing, or coating, to achieve the desired finish.
Additional finishing can increase production time and costs.
3. Production Speed & Scalability
While 3D printing is ideal for low-volume production, it may not yet compete with traditional methods for large-scale production.
Hybrid approaches combining CNC machining or injection moulding with 3D printing are emerging to address this.
4. Regulatory and Certification Challenges
Industries like aerospace, healthcare, and defence have strict regulatory requirements.
Companies must ensure compliance with industry standards and material certifications.
Future Trends in Low Volume Manufacturing with 3D Printing
1. Advancements in Multi-Material Printing
The development of multi-material 3D printing will enable the production of complex, high-performance components.
Industries such as electronics and robotics will benefit from integrated conductive and structural materials.
2. AI-Driven Design & Automation
Generative design software and AI-driven optimisations will improve the efficiency and functionality of 3D-printed parts.
AI will help automate material selection, quality control, and design iterations.
3. Increased Use of Metal 3D Printing
Metal additive manufacturing (AM) is advancing, making it more accessible for small-scale production.
Ideal for industries requiring high-strength, heat-resistant components.
4. On-Demand Manufacturing Networks
The rise of distributed manufacturing platforms allows businesses to order 3D-printed parts on demand.
Reduces the need for in-house production and lowers logistics costs.
5. Sustainability and Eco-Friendly Materials
The development of biodegradable and recyclable 3D printing materials will enhance sustainability.
Energy-efficient 3D printing technologies are being explored to reduce environmental impact.
Conclusion
Low-volume manufacturing with 3D printing is transforming industries by offering cost-effective, flexible, and sustainable production solutions. With continued advancements in materials, automation, and AI-driven design, 3D printing is poised to become an even more powerful tool for low-volume production.
Companies that embrace this technology can benefit from faster innovation cycles, reduced costs, and greater customisation, ensuring a competitive edge in today’s fast-evolving market. As 3D printing continues to advance, low-volume manufacturing will only become more efficient, scalable, and accessible to a wider range of industries.
The Future of 3D Printing: Industry Trends, Common Questions, and Case Studies
Introduction
3D printing technology is transforming industries, from manufacturing and healthcare to fashion and automotive. As businesses and individuals explore its potential, many questions arise about how it works, where it’s heading, and real-world applications. This blog post will address common questions, discuss key industry trends, and highlight case studies showcasing the power of 3D printing.
1. Common Questions About 3D Printing
What is 3D Printing?
3D printing, also known as additive manufacturing, is a process of creating three-dimensional objects layer by layer using digital designs. Unlike traditional subtractive manufacturing, which involves cutting away material from a solid block, 3D printing builds objects from the ground up using various materials such as plastic, metal, resin, and even bio-materials.
What Are the Different Types of 3D Printing Technologies?
There are several 3D printing techniques, but the most commonly used include:
•Fused Deposition Modeling (FDM): Uses thermoplastic filaments melted and layered to create objects.
•Stereolithography (SLA): Uses UV light to cure liquid resin into solid structures.
•Selective Laser Sintering (SLS): Utilizes a laser to fuse powdered material (often nylon) into solid objects.
•Metal 3D Printing (DMLS/SLM): Uses high-powered lasers to fuse metal powders for industrial applications.
What Are the Benefits of 3D Printing?
•Customization: Enables the creation of highly customized products, from prosthetic limbs to intricate jewelry designs.
•Speed and Efficiency: Rapid prototyping allows businesses to test designs quickly before full-scale production.
•Cost-Effectiveness: Reduces material waste and eliminates the need for expensive molds and tooling.
•Sustainability: Some 3D printing technologies use recycled materials, reducing environmental impact.
2. Industry Trends in 3D Printing
a) Growth of Industrial 3D Printing
While 3D printing started as a prototyping tool, it is now used for full-scale manufacturing in industries such as aerospace, automotive, and healthcare. Companies like Boeing and Tesla are integrating 3D-printed components into their production processes.
b) Advancements in 3D Printing Materials
New materials, including carbon fiber composites, biodegradable filaments, and bioprinting materials, are expanding the possibilities of 3D printing. These innovations improve strength, durability, and environmental sustainability.
c) 3D Printing in Healthcare
The healthcare industry is benefiting from 3D printing through:
•Patient-Specific Implants: Custom-made orthopedic and dental implants.
•Bioprinting: Research into printing human tissues and organs for transplantation.
•Medical Equipment: Low-cost, customized prosthetics and surgical tools.
d) Sustainability and Eco-Friendly 3D Printing
With growing environmental concerns, many 3D printing companies are focusing on:
•Using recycled and biodegradable materials.
•Developing zero-waste manufacturing processes.
•Implementing circular economy principles, where old 3D-printed items are recycled into new products.
e) 3D Printing in Construction
3D-printed homes and infrastructure are gaining traction as companies develop faster, cheaper, and more sustainable building methods. The first 3D-printed communities are being developed in areas facing housing shortages.
3. Case Studies: Real-World Applications of 3D Printing
Case Study 1: 3D Printing in Aerospace
Company: Airbus
Airbus has integrated 3D printing into its aircraft production process, using it to create lightweight components that reduce overall weight and improve fuel efficiency. The company has successfully produced titanium 3D-printed brackets used in A350 aircraft.
Case Study 2: 3D Printing in Healthcare
Organization: The University of Michigan
Surgeons at the University of Michigan successfully used 3D printing to create a customized airway splint for a baby with life-threatening breathing issues. The device was bioresorbable, meaning it would dissolve in the body over time.
Case Study 3: 3D Printing in Fashion
Brand: Adidas
Adidas has launched its Futurecraft 4D sneakers, which feature 3D-printed midsoles designed for optimal comfort and performance. This move highlights the role of 3D printing in mass customization and sustainable manufacturing in the fashion industry.
Conclusion
3D printing is no longer just an emerging technology—it’s a game-changer across multiple industries. From healthcare to aerospace and fashion, businesses are leveraging its capabilities to create innovative, cost-effective, and sustainable solutions. As materials and technologies continue to advance, the future of 3D printing looks more promising than ever.
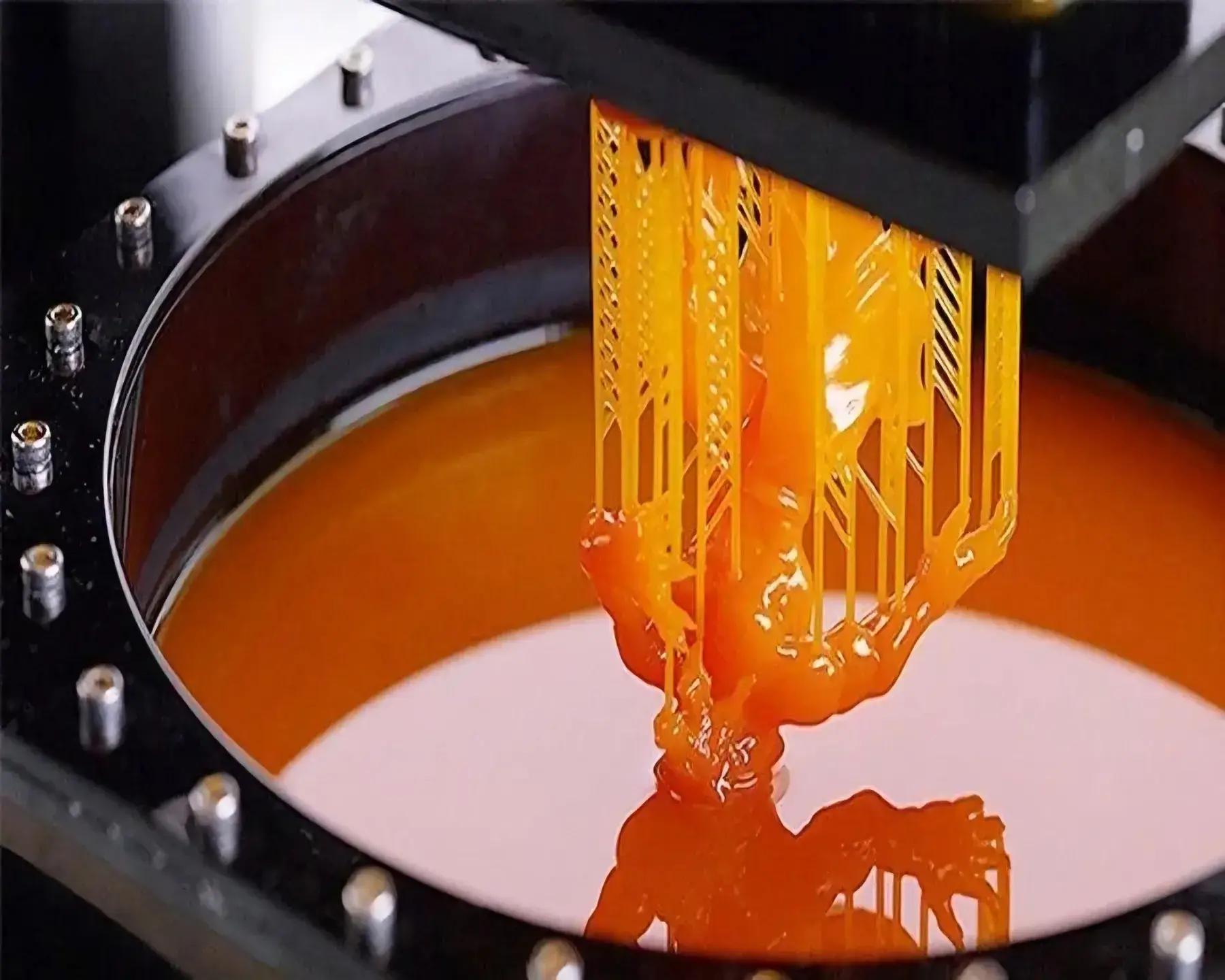
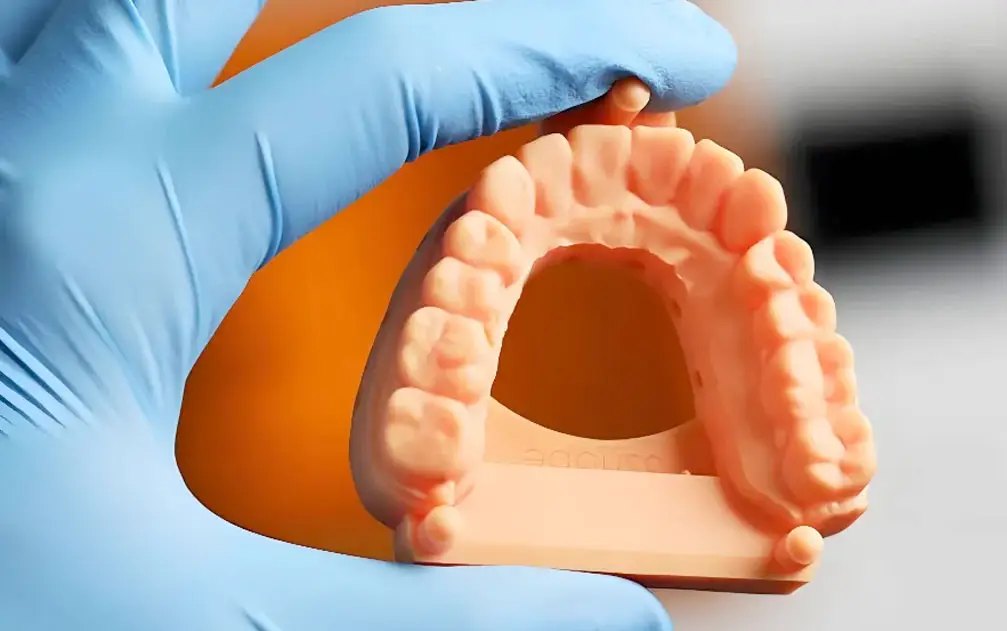